

Read error modbus poll Pc#
But if I tapping the A & B line signal when I send read holding register function from PC using modbus poll (give timeout error) I got some weird signal: I've tapping the A & B signal using logic analyzer, if I send some character from uC to RS-485 (but not connected to PC), the character showing correctly on A & B line.
Read error modbus poll code#
Try changing the RS-485 to RJ-45 converter board (just in case it broke), the phenomena just repeat.Ĭan someone give me some advice on what could be the possible cause?Īlso, I'm not sure about this, in Modbus RTU format, at the start and end there should be 28 bit (at least 3 1/2 character length), but should the micro firmware code care about this since at the PC use modbuspoll tool? I've tried changed UART baud rate from 9600 to 115200.
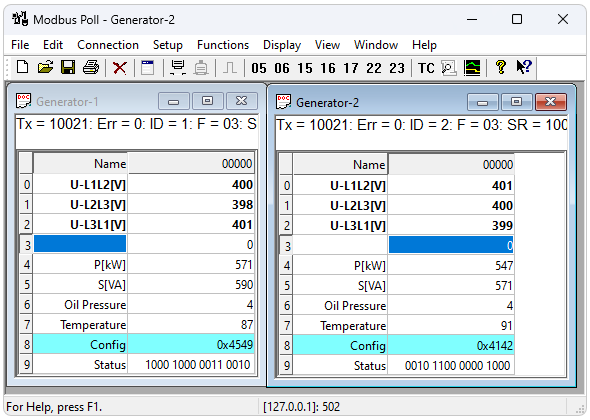
But after I send some of the motor settings using Modbus write single register function then the motor start running, it was then the Modbus communication always timeout error.Īnd once the timeout error happens, the next time I turn on the system again it will keep giving timeout error. If the slave device takes the requested action without error, it returns. When I use function code 03, TxD and RxD on Moxa connector are blinking, but only RxD is blinking on.
Read error modbus poll software#
(wiring can be found in attachment) Settings of Modbus poll software can be found in attachment.

I am using Moxa 1150 with DB9 connector to connect PLC with PC. PIC24 -> UART -> IC MAX3471 -> RS-485 to RJ-45 converter -> RJ-45 to USB -> PC (running modbuspoll tool)Īt first, the Modbus read holding register function and write single register function is working. For example, the Read Holding Registers command has the function code. Now, I want to test communication additionally with Modbus poll software on PLC. Error Code P499 shows any Errors that are generated by. The motor setting like the angle, delay, start/stop, duty cycle, etc will be sent from PC using Modbus to PIC24. The error message is displayed across the top of the panel screen. My task is to control a DC motor using micro PIC24. Note: When using the Modbus Poll software, addressing should be set to Protocol Addresses (Base 0) under the Display menu. Anyone very experienced with Modbus & RS-485? If your application can read & write bytes to a separate PC running the ‘Modbus Slave’ application, you will be able to read & write bytes to the modules.
